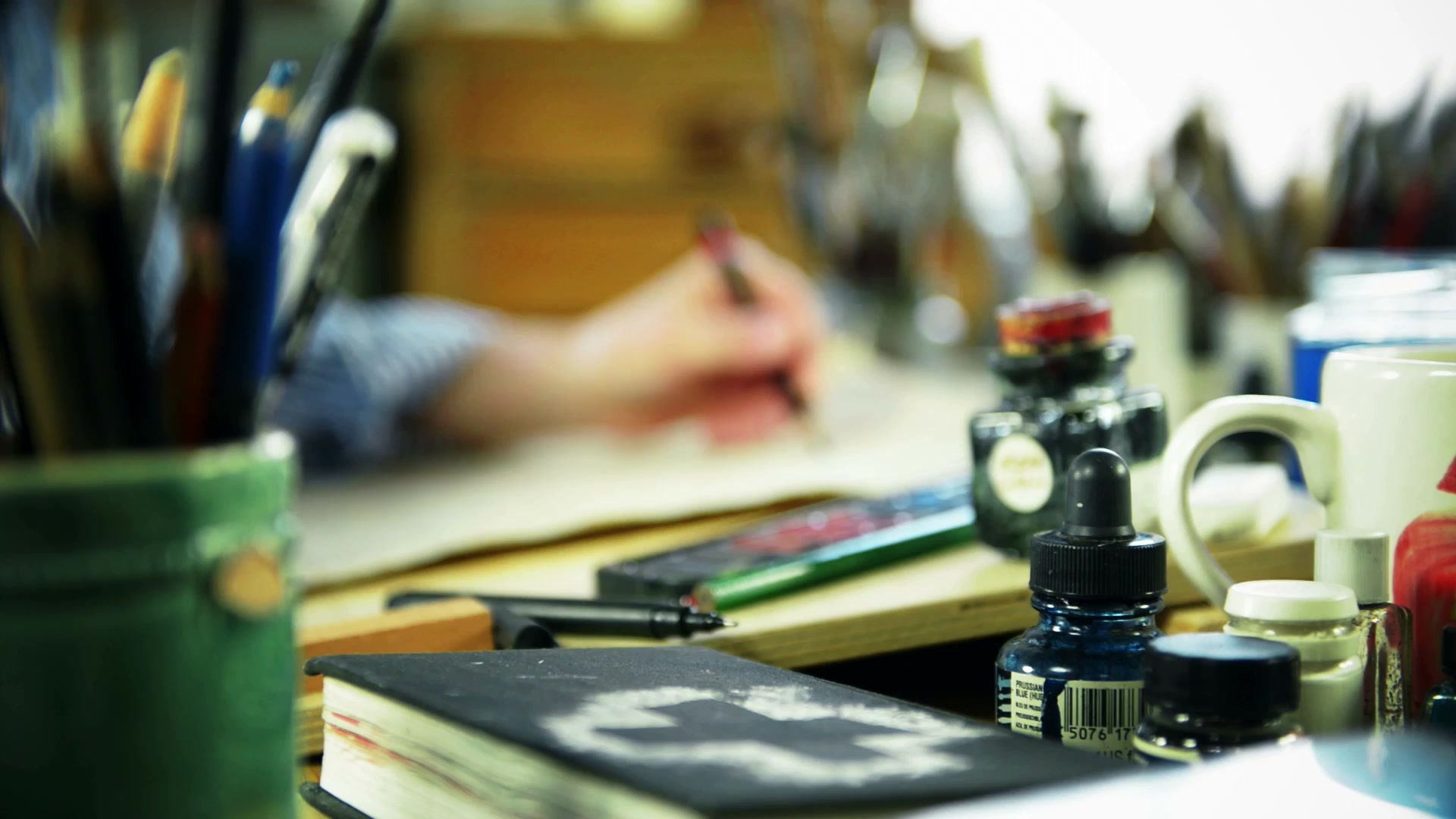
PROJECT WORK ASSISTANCE
Gain Industry Work Experience on
Final year PROJECT work
We support S6, S7 Mechanical Engineering students to pitch - in with relevant project titles related to mobility product design for vehicle safety, performance and integration. The students are provided with an opportunity to obtain work experience while studying and completing the project work, so the student get placed immediately after the graduation with a product design services or OEM, Tier-1 manufacturing organizations. Each project is a balance of hands-on design and in-depth simulation, allowing the students to explore practical automotive engineering challenges.
The project titles are chosen based on the industrial practices and job opportunities across PAN India & Abroad on various topics related to vehicle performance enhancement.
Our expertise:
-
Define the problem identification of the automotive product.
-
Map the Project timeline, Cost and Effort estimation.
-
Detailing the Product Conceptual as per root cause study.
-
Defining the Product Definition process and Tools.
-
Define the VA/VE & Cost engineering proposals.
-
Define the Manufacturing process, (3D printing or fabrication)
-
Define the Product Verfification and Validation plans and testing.
-
Support for the Report results and Project Report Preperation.

Design and Simulation of a Lightweight Automotive Component
Overview: Focus on designing a lightweight but structurally strong automotive product.
Tools: CATIA for the 3D modeling, ANSYS for Finite Element Analysis (FEA) to perform stress, strain, and fatigue analysis.
Goal: Reduce the weight of the component without compromising safety or durability, helping to improve overall fuel efficiency and vehicle performance.
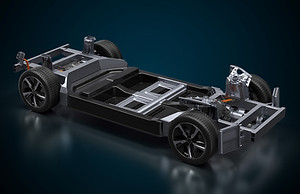
Design and Optimization of a Lightweight Automotive Chassis
Overview: Design a lightweight yet strong automotive chassis that can reduce vehicle weight while ensuring the required safety and structural integrity.
Tools: CATIA for the detailed design of the chassis components (cross-members, reinforcements, etc.) and ANSYS for Finite Element Analysis (FEA) to assess stress, strain, and fatigue properties.
Goal: Optimize material selection and geometry for weight reduction while maintaining or enhancing the vehicle’s safety and performance.

Development of a Vehicle Frame with Integrated Composite Materials
Overview: Investigate and design a vehicle frame that uses composite materials (such as carbon fiber or fiberglass) for weight reduction without sacrificing strength and safety.
Tools: CATIA for modeling the frame and integration of composite materials. ANSYS for FEA to analyze the behavior of composite materials under various loading conditions (static and dynamic).
Goal: Design a frame structure that is lightweight and robust, taking advantage of the unique properties of composite materials such as high strength-to-weight ratios.

Aerodynamic Optimization of Vehicle
Exterior for Fuel Efficiency
Overview: Design the vehicle’s exterior body to minimize drag and maximize fuel efficiency, especially for high-performance or electric vehicles.
Tools: CATIA for surface design, body contours, and integration with other vehicle components (windows, doors, etc.). ANSYS Fluent or CFX for Computational Fluid Dynamics (CFD) to simulate air flow around the vehicle.
Goal: Optimize the body design to reduce aerodynamic drag, improve stability, and enhance fuel efficiency.

Overview: Use CATIA to design a streamlined car body that minimizes drag and maximizes fuel efficiency.
Tools: CATIA for aerodynamic shape design, ANSYS Fluent or CFX for Computational Fluid Dynamics (CFD) analysis.
Goal: Optimize the car's aerodynamics to reduce air resistance and improve fuel efficiency or speed.
Design of an Aerodynamic Car Body

Development of an Active Aerodynamic
System for Vehicle Body
Overview: Design an active aerodynamic system that adjusts the vehicle's body components (e.g., rear spoilers, active grilles) based on speed and driving conditions to reduce drag and improve stability.
Tools: CATIA for the design of moving body components and the integration of actuators. ANSYS for CFD to analyze airflow and aerodynamic performance of the moving components.
Goal: Enhance vehicle performance by dynamically adjusting aerodynamic features based on real-time conditions.
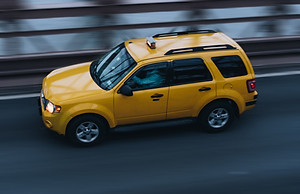
Aerodynamic Optimization of a Vehicle
Roof and Side Panels
Overview: Improve the aerodynamics of a vehicle by designing the roof and side panels to reduce drag and improve fuel efficiency.
Tools: CATIA for designing the smooth contours of the roof and side panels, integrating the design with the overall vehicle body. ANSYS Fluent (CFD) for analyzing airflow around the vehicle’s exterior.
Goal: Reduce drag and improve vehicle stability at high speeds by optimizing the vehicle’s roof and side panel design.

Design and Analysis of an Electric Vehicle (EV) Battery Housing
Overview: Design a battery housing structure for an electric vehicle, focusing on safety, heat dissipation, and compactness.
Tools: CATIA for design and ANSYS for thermal and structural analysis.
Goal: Ensure the housing provides adequate protection for the battery, minimizes heat generation, and is compact for integration into the vehicle design.

Design of a Crashworthy Vehicle Frame
Overview: Focus on designing a vehicle frame that maximizes passenger safety in the event of a crash.
Tools: CATIA for 3D modeling, ANSYS for crash simulation and FE
Goal: Improve crashworthiness by simulating real-world collision scenarios and optimizing the frame for energy absorption and protection.

Crashworthiness Analysis and Design of a Vehicle Body Structure
Overview: Focus on improving the crashworthiness of a vehicle body by optimizing the design for better energy absorption during front, side, and rear collisions.
Tools: CATIA for modeling the entire body structure, including the crumple zones, safety cells, and reinforcement areas. ANSYS for crash simulations (explicit dynamics) and FEA to simulate the crash event and assess the body structure's energy absorption capacity.
Goal: Enhance passenger safety by improving the energy dissipation characteristics and minimizing intrusion into the passenger compartment.

Vehicle Cabin Noise Reduction through Material Selection and Design
Overview: Investigate the impact of material selection and design changes on reducing cabin noise in a vehicle.
Tools: CATIA for the design of interior components (such as door panels, dash, etc.), ANSYS for acoustic simulation.
Goal: Optimize material selection and geometry to minimize road and engine noise inside the cabin.
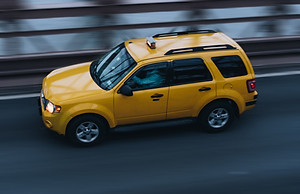
Design and Analysis of a Vehicle Roof Structure with Focus on Safety and Weight Reduction
Overview: Design an innovative roof structure that ensures both safety (in rollover accidents) and weight reduction, potentially using advanced materials or hybrid designs.
Tools: CATIA for roof structure design, integrating reinforcements, lightweight materials, and safety features. ANSYS for crash simulations, FEA to evaluate stress distribution, and buckling analysis to assess rollover protection.
Goal: Enhance the roof structure to withstand forces from a rollover accident while minimizing weight through the use of advanced materials.

Design and Simulation of a Modular Vehicle Body System
Overview: Develop a modular body system for a vehicle that allows for easy replacement or modification of parts, improving flexibility in production and reducing manufacturing costs.
Tools: CATIA for the modular design of body components that can be easily swapped or customized. ANSYS for FEA to simulate how the modular body system handles loads and forces during driving.
Goal: Create a flexible, cost-efficient body system that maintains the vehicle’s performance and safety while reducing production time and costs.

Design and Simulation of an Automotive
Side-Impact Protection System
Overview: Develop a side-impact protection system for the vehicle body that can minimize occupant injury during side collisions.
Tools: CATIA for the design of the side door structure, reinforcements, and integration with airbag systems. ANSYS for crash simulation (side-impact), structural analysis, and energy absorption during impact.
Goal: Improve occupant safety by designing a side-impact protection system that minimizes intrusion and optimizes energy absorption.

Design of an Automotive Door with Focus
on Safety and Weight Reduction
Overview: Design an automotive door that is lightweight, cost-effective, and capable of absorbing impact energy during collisions to protect passengers.
Tools: CATIA for detailed design of the door frame, outer panel, and reinforcement structures. ANSYS for stress analysis, impact simulations, and fatigue testing.
Goal: Minimize the weight of the door while maintaining high crashworthiness and safety standards.

Analysis and Design of an Automotive
Seat Frame
Overview: Design a seat frame for a vehicle that provides comfort, safety (in crash conditions), and is lightweight.
Tools: CATIA for the seat frame design, including geometry for structural integrity and integration with safety features. ANSYS for FEA to evaluate the frame’s strength, fatigue resistance, and performance during crash tests.
Goal: Optimize the seat frame design for comfort and safety while reducing weight and material usage.
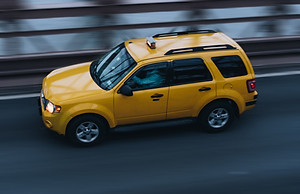
Design of a Vehicle Roof Railing System
for Cargo Carrying
Overview: Design a roof railing system that allows for the safe carrying of cargo, providing strength and durability while integrating seamlessly with the vehicle roof.
Tools: CATIA for designing the roof rails, considering the attachment points, material strength, and user accessibility. ANSYS for structural analysis to ensure that the system can withstand the forces from cargo during braking or sudden maneuvers.
Goal: Ensure the roof railing system is functional, durable, and lightweight, with minimal impact on vehicle aerodynamics.

Design and Stress Analysis of a Car Fender
Overview: Design a car fender that provides structural strength, is lightweight, and integrates with the rest of the vehicle body.
Tools: CATIA for creating the 3D model of the fender, considering its shape, material, and fitment with the rest of the vehicle. ANSYS for FEA to simulate how the fender behaves under external forces (e.g., road debris impacts, vibration).
Goal: Develop a fender that balances strength, weight, and cost, while ensuring durability and safety.
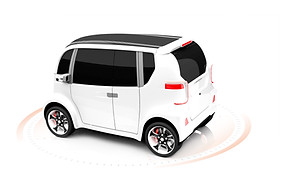
Design of a Car Boot Lid with Focus on
Weight and Durability
Overview: Design a car boot lid that is lightweight, durable, and meets the strength requirements for everyday use (e.g., opening/closing, impact resistance).
Tools: CATIA for creating the boot lid structure, including internal reinforcements, hinges, and locking mechanism. ANSYS for stress analysis, fatigue testing, and impact simulations (e.g., from objects falling on the lid).
Goal: Create a boot lid that is both lightweight and strong, while considering ease of manufacturing.
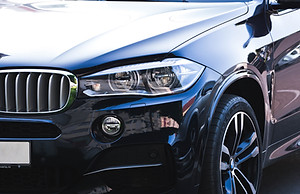
Design and Structural Analysis of a Vehicle Bumper System
Overview: Design a front/rear vehicle bumper that provides impact resistance while being lightweight and cost-effective.
Tools: CATIA for the design of the bumper, considering material selection and integration with other body parts (e.g., front grill, fender). ANSYS for Finite Element Analysis (FEA) to simulate the bumper’s performance during impact scenarios.
Goal: Optimize the bumper for energy absorption, durability, and cost reduction while ensuring it meets regulatory standards.

Design and Simulation of a Wheel Arch to Minimize Mud and Water Splash
Overview: Design a wheel arch that reduces the amount of mud, water, and debris splashed onto the vehicle body, improving aerodynamics and cleanliness.
Tools: CATIA for designing the wheel arch with consideration for shape, material, and attachment points. ANSYS Fluent (CFD) to analyze the airflow around the wheel and its interaction with mud and water during driving.
Goal: Minimize splash and improve the vehicle’s aerodynamics by optimizing the shape and material properties of the wheel arch.

Design and Analysis of a Vehicle Skid Plate
Overview: Design a skid plate for the vehicle’s underbody that protects the engine and transmission from rocks, debris, and impact during off-road driving.
Tools: CATIA for the design of the skid plate, focusing on durability, ease of mounting, and material selection. ANSYS for impact simulation and stress analysis to assess the skid plate’s resistance to road debris.
Goal: Ensure the skid plate provides adequate protection without significantly adding weight to the vehicle.

Design & Validation of Front Bumper Beam
for Pedestrian Protection.
Overview: Design an bumper beam in a suitable material for a passenger vehicle, focusing on pedestian safety.
Tools: CATIA for the 3D modeling of the bumper beam and its components, possibly integrating with FEM.
Goal: Create a bumper beam that integrates seamlessly with the vehicle's FEM for modularity.

Development of a Smart Dashboard Interface Design
Overview: Design an intuitive and futuristic digital dashboard interface for a vehicle, focusing on user experience and safety.
Tools: CATIA for the 3D modeling of the dashboard and its components, possibly integrating with software tools for UI/UX design.
Goal: Create a dashboard that integrates seamlessly with the vehicle's infotainment and safety systems.
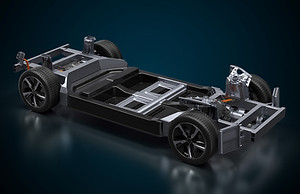
Design and Analysis of a Vehicle Chassis for Autonomous Vehicles
Overview: Focus on designing a chassis optimized for autonomous vehicles, where structural integrity and safety are critical.
Tools: CATIA for design, ANSYS for FEA to analyze the chassis under various loading conditions.
Goal: Create a strong, lightweight chassis that can support the advanced sensors and computing systems in autonomous vehicles.
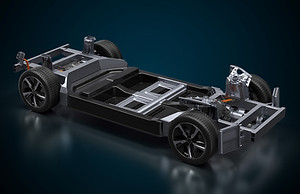
Design and Optimization of a Lightweight Automotive Chassis
Overview: Design a lightweight yet strong automotive chassis that can reduce vehicle weight while ensuring the required safety and structural integrity.
Tools: CATIA for the detailed design of the chassis components (cross-members, reinforcements, etc.) and ANSYS for Finite Element Analysis (FEA) to assess stress, strain, and fatigue properties.
Goal: Optimize material selection and geometry for weight reduction while maintaining or enhancing the vehicle’s safety and performance.